Understanding Concrete Mixing Plants: A Key Component of Successful Construction Projects
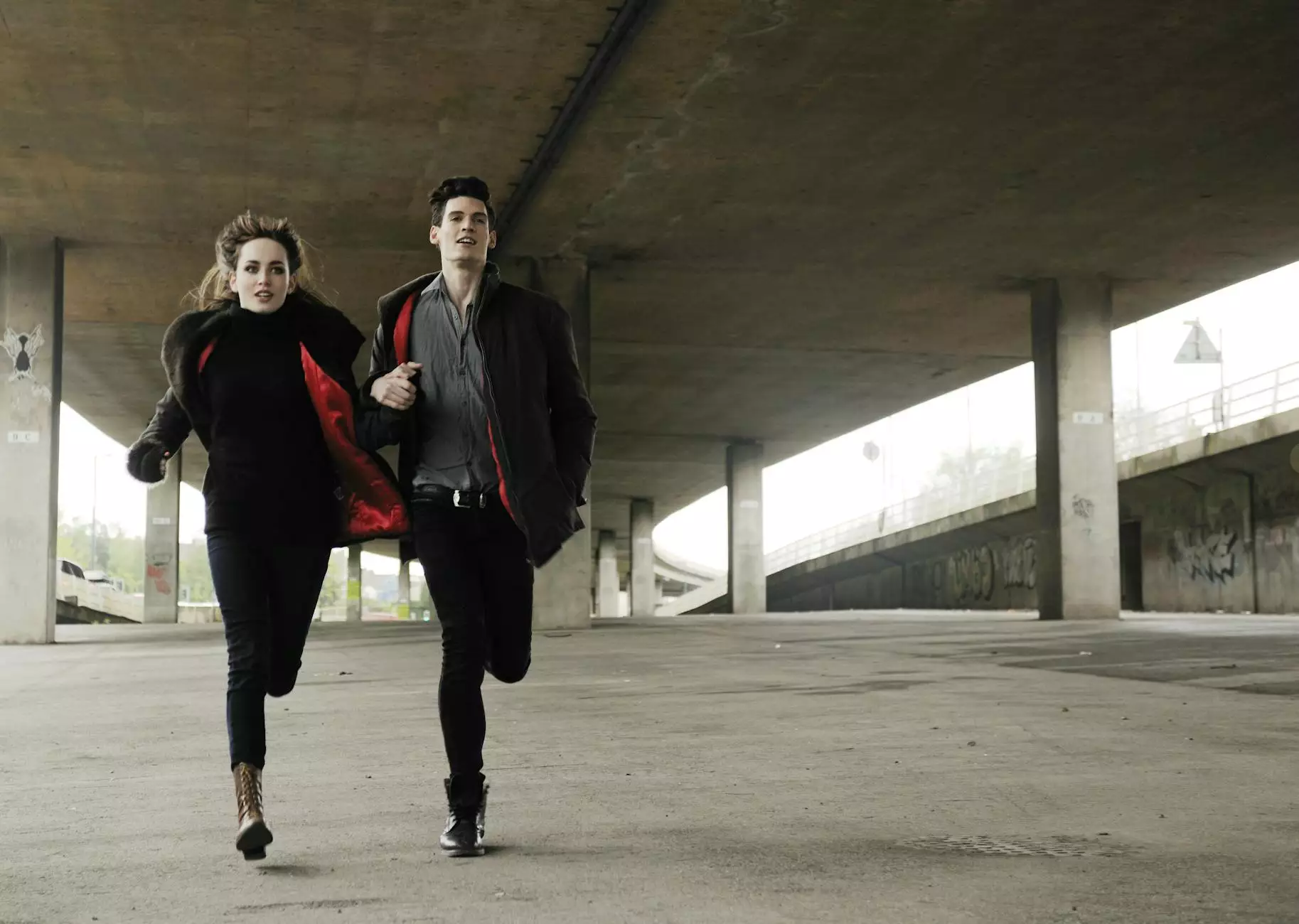
In today's rapidly evolving construction industry, the demand for high-quality, durable materials has never been greater. At the forefront of this demand is the concrete mixing plant, a vital equipment that significantly enhances the efficiency and quality of the construction process. This article delves into what concrete mixing plants are, their benefits, types, and their impact on the construction industry.
What is a Concrete Mixing Plant?
A concrete mixing plant, often referred to as a concrete batch plant, is a facility where various ingredients including water, cement, sand, gravel, and additives are combined to produce concrete. These plants can vary in size and complexity, ranging from small, manual batch plants to large, fully automated commercial facilities.
Components of a Concrete Mixing Plant
Concrete mixing plants consist of several key components, each playing an essential role in the concrete production process:
- Cement Silos: These are large storage tanks that hold cement until it is needed for mixing.
- Aggregate Bins: Used to store various types of aggregates like sand and gravel, which are crucial in concrete production.
- Mixing Unit: This is where all the ingredients are combined to produce concrete. The mixing unit can be either a pan type or a drum type mixer.
- Control System: Modern concrete mixing plants are equipped with sophisticated control systems that automate the entire mixing process.
- Water Supply System: Accurate water dosage is critical in producing quality concrete, and this system ensures the right amount is added during mixing.
Types of Concrete Mixing Plants
Concrete mixing plants come in various types, each serving specific needs and project requirements. Here are the primary types:
1. Stationary Concrete Mixing Plant
These plants are typically installed in a permanent location and are ideal for large construction projects. They offer high production capacity and are designed for continuous operation. Stationary plants are commonly used for projects such as highways, bridges, and large commercial buildings.
2. Mobile Concrete Mixing Plant
Mobile plants are compact and can be easily transported from one job site to another. They provide flexibility and are perfect for projects that require frequent relocation. Mobile plants have a lower production capacity but are advantageous for smaller projects and sites with space constraints.
3. Compact Concrete Mixing Plant
Designed for efficiency and rapid setup, compact concrete mixing plants combine mobility with the operational capability of larger plants. They are suitable for both small and medium-scale projects, providing quality concrete with minimal installation time.
Advantages of Using Concrete Mixing Plants
The integration of concrete mixing plants in construction projects presents numerous benefits:
- Quality Control: Concrete mixing plants ensure that the concrete produced meets specific quality standards through accurate measurement and mixing of ingredients.
- Cost Efficiency: By producing concrete on-site, companies can save on transport costs and reduce waste, leading to overall lower project expenses.
- Increased Productivity: The automation and efficiency of modern concrete mixing plants enable higher production rates compared to manual mixing.
- Flexibility: Various types of plants, including mobile options, allow for concrete production to occur closer to the job site, minimizing delays.
- Environmentally Friendly: Newer mixing plants are designed to minimize waste and incorporate sustainable practices, such as recycling water.
How Concrete Mixing Plants Transform the Construction Industry
The use of concrete mixing plants has revolutionized the construction industry in several ways:
1. Enhanced Construction Speed
The ability to produce large quantities of concrete quickly means that projects can move forward more rapidly. Delays caused by waiting for materials to arrive are minimized, enabling contractors to meet tighter deadlines and improve overall project timelines.
2. Improved Material Consistency
Consistent concrete quality is essential for the integrity and longevity of structures. Concrete mixing plants utilize advanced technology to ensure that each batch of concrete meets stringent specifications, reducing the likelihood of structural failures and costly repairs.
3. Customization and Versatility
Today's plants allow for easy adjustments in formulas and mixtures, enabling builders to customize concrete blends for specific applications, such as high-strength concrete for skyscrapers or lightweight concrete for precast applications.
Choosing the Right Concrete Mixing Plant
When selecting a concrete mixing plant, several factors should be considered to ensure it meets the project's needs:
- Production Capacity: Assess the volume of concrete required for your project to determine the appropriate size of the plant.
- Type of Mixing Plant: Decide between stationary, mobile, or compact plants based on project size and location.
- Technological Features: Look for plants with modern automation and control systems for optimal performance and monitoring.
- Budget: Consider the initial investment and long-term operational costs, ensuring it aligns with your project's financial plan.
- Supplier Reputation: Choose a reputable supplier, such as Polygonmach, known for quality equipment and excellent customer support.
Maintenance and Care for Concrete Mixing Plants
Regular maintenance of concrete mixing plants is essential to ensure they operate efficiently and have a long lifespan. Here are some best practices:
- Routine Inspections: Conduct regular checks on key components, including the mixing unit, control systems, and batching equipment.
- Cleaning: After each use, clean the plant thoroughly to prevent concrete buildup and maintain operational efficiency.
- Lubrication: Ensure that all moving parts are properly lubricated to reduce wear and tear and enhance performance.
- Professional Servicing: Schedule periodic professional assessments and servicing to catch potential issues early.
- Record Keeping: Maintain detailed records of maintenance activities, repairs, and equipment usage to track efficiency and inform future decisions.
The Future of Concrete Mixing Plants
As technology continues to advance, the future of concrete mixing plants looks promising:
1. Automation and AI
Emerging technologies such as artificial intelligence and machine learning are poised to further automate plant operations, improving efficiency and minimizing human error.
2. Sustainability Innovations
With increasing awareness of environmental issues, the development of greener concrete mixing processes and materials will likely become a focal point, contributing to sustainable construction practices.
3. Modular Construction Trends
As the demand for modular construction rises, concrete mixing plants will need to adapt to supply specialized concrete tailored for prefabricated building components.
Conclusion
Concrete mixing plants are indispensable in today's construction landscape, enhancing the efficiency, quality, and sustainability of building projects. Whether you are involved in large-scale developments or smaller constructions, understanding the benefits, types, and future trends of concrete mixing plants will equip you with invaluable knowledge to make informed decisions. To explore high-quality concrete mixing plants, consider partnering with a trusted provider like Polygonmach, who offers state-of-the-art solutions tailored to meet the ever-evolving demands of the construction industry.