Understanding Metal Die Casting: Transforming Industries with Precision
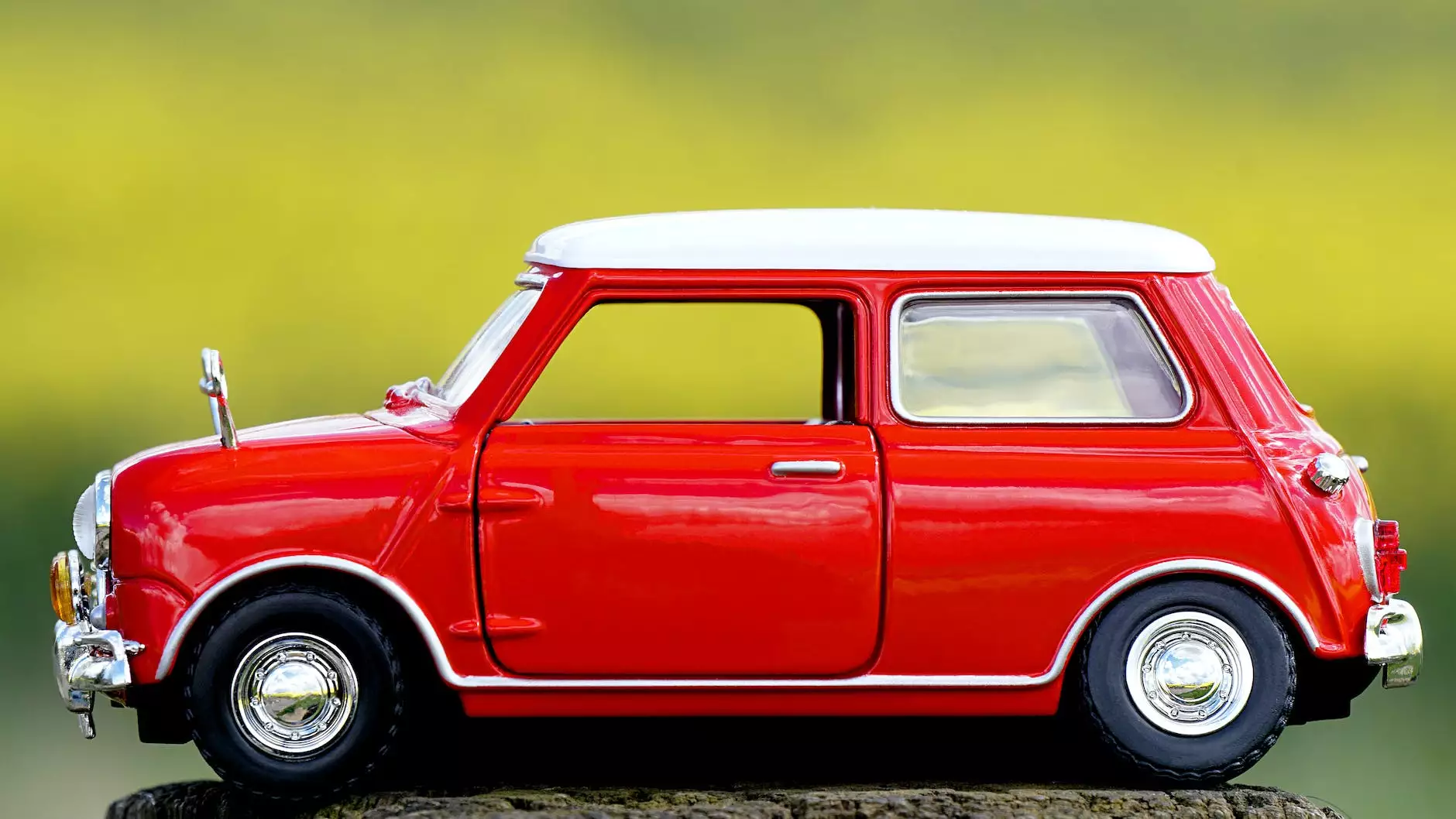
Metal die casting is an essential manufacturing process that has revolutionized the way various industries create complex metal parts. This article covers everything from the fundamental principles of die casting to its vast applications across different sectors. By understanding this process, businesses can leverage the advantages it offers, enhancing quality, efficiency, and profitability.
What is Metal Die Casting?
At its core, metal die casting involves forcing molten metal into a mold, where it solidifies to form a specified shape. This process is known for producing high volumes of precisely engineered parts, making it a preferred method in many sectors, including automotive, aerospace, and consumer goods.
The Evolution of Metal Die Casting
The history of die casting dates back to the late 19th century, with significant advancements made throughout the 20th century. Initially, die casting was restricted to small parts, primarily used for manufacturing toys and small tools. However, improvements in technology and materials broadened its applications extensively.
The Die Casting Process: A Step-by-Step Guide
The metal die casting process can be broken down into several key steps:
- Mold Creation: High-quality molds are crafted from hard materials, typically steel, to withstand repeated use.
- Melting the Metal: Various metals, including aluminum, zinc, and magnesium, are melted in a furnace.
- Injecting the Metal: The molten metal is injected under high pressure into the prepared mold cavity.
- Cooling and Solidification: The metal cools and solidifies quickly within the mold.
- Mold Removal: Once the part has cooled, it is removed from the mold, often requiring minimal finishing.
Advantages of Metal Die Casting
Implementing metal die casting presents numerous advantages, significantly impacting production capabilities:
- High Precision and Detail: The process allows for intricate designs and excellent dimensional accuracy.
- Superior Strength: Cast metal parts exhibit high strength and durability, ideal for demanding applications.
- Cost-Effectiveness: Mass production reduces per-unit costs, making it a financially viable option.
- Rapid Production Rates: The speed of the die casting process meets high demand without compromising quality.
- Material Efficiency: Minimal waste is generated, as excess material can be recycled and reused.
Common Applications of Metal Die Casting
Metal die casting is utilized across various industries. Here are some common applications:
- Automotive Industry: Components such as engine blocks, transmission cases, and wheels.
- Aerospace Sector: Parts that require high strength-to-weight ratios, like brackets and housings.
- Consumer Electronics: Enclosures for devices, connectors, and heat sinks.
- Industrial Equipment: Create housings and frames for machinery and tools.
- Home Appliances: Components in washing machines, refrigerators, and other devices.
Materials Used in Metal Die Casting
Several metals are commonly used in die casting, each offering distinct advantages:
- Aluminum: Lightweight, corrosion-resistant, and excellent thermal conductivity.
- Zinc: Offers good strength and ductility, ideal for complex shapes.
- Magnesium: Known for its excellent strength-to-weight ratio, often used in automotive parts.
Quality Control in Metal Die Casting
Maintaining quality in metal die casting is critical for ensuring the performance of the final product. Various methods are employed to monitor quality throughout the process:
- Dimensional Checks: Regular measurements to ensure parts meet specified tolerances.
- Non-Destructive Testing: Techniques like X-ray or ultrasonic testing to identify internal defects.
- Surface Inspections: Examination of surface quality to detect imperfections.
The Future of Metal Die Casting
As industries evolve, the future of metal die casting appears promising:
- Automation and Robotics: Enhanced automation will streamline processes and improve efficiency.
- Advanced Materials: Research in new alloys could lead to better performance and versatility.
- 3D Printing Integration: Combining die casting with 3D printing could revolutionize prototyping and production techniques.
Choosing the Right Die Casting Partner
For businesses considering metal die casting, selecting the right partner is paramount. Here are key factors to consider:
- Experience and Expertise: A reputable partner will have years of experience in the industry.
- Quality Assurance: Ensure they have robust quality control measures in place.
- Technology and Equipment: State-of-the-art facilities can offer advanced capabilities.
- Responsive Communication: Strong partnerships require open and effective communication throughout the project.
Conclusion
In conclusion, metal die casting is a transformative process that delivers efficiency and precision in industrial manufacturing. With its numerous applications and increasing importance, it is essential for businesses within related fields to understand the benefits and processes involved. As technology continues to advance, the potential of die casting will undoubtedly grow, paving the way for innovative products and solutions across industries.
For more information on metal die casting services, or to partner with experts in the field, visit deepmould.net. Together, we can achieve manufacturing excellence and innovation.