Understanding Central Lubrication System Fittings
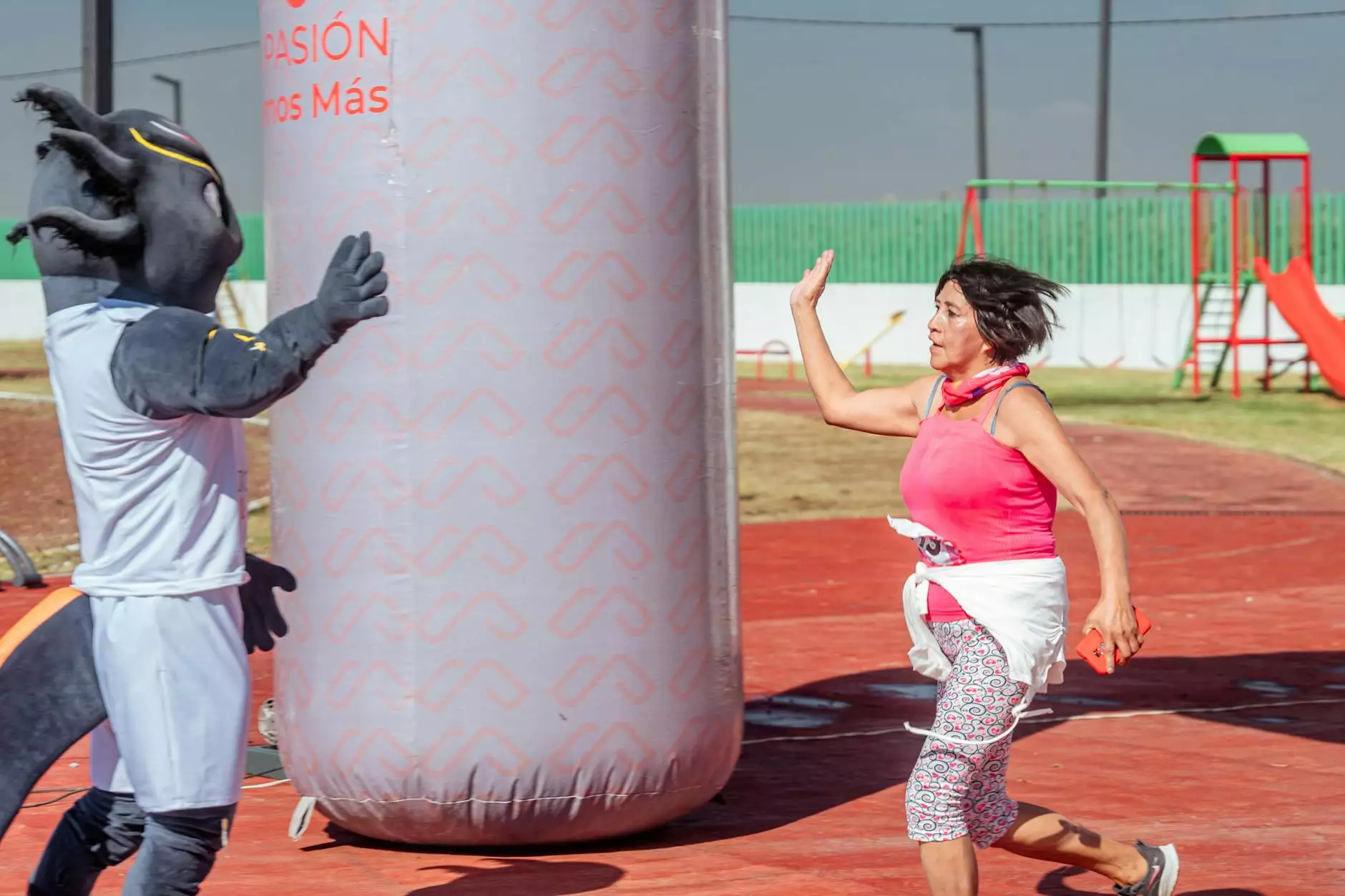
What Are Central Lubrication System Fittings?
Central lubrication system fittings are critical components in the machinery of various industries, ensuring that lubricants are distributed efficiently to machinery parts. These fittings allow for precise control and efficient lubrication, which is vital for the longevity and proper functioning of equipment.
The Importance of Central Lubrication Systems
In industrial settings, machinery operates under high stress conditions. The absence of adequate lubrication can lead to wear, overheating, and ultimately, equipment failure. Here are several reasons why central lubrication systems and their fittings are essential:
- Efficiency: Central systems streamline the lubrication process, reducing the need for manual lubrication.
- Cost Savings: By maintaining machinery in better condition, businesses can save significantly on repair and replacement costs.
- Time Savings: Automated systems allow operators to focus on more critical tasks rather than spending time on manual lubrication.
- Enhanced Safety: Reducing human intervention in lubrication decreases the likelihood of accidents.
Types of Central Lubrication System Fittings
Central lubrication system fittings come in various types, each designed for specific applications. Here are some of the most common types:
1. Grease Fittings
Grease fittings, also known as zerk fittings, facilitate the easy injection of lubricant into machinery. They are crucial for ensuring that moving parts are adequately supplied with grease.
2. Oil Fittings
Designed to handle liquid lubricant, oil fittings are vital for any machinery requiring proper oil circulation. These fittings maintain consistent oil flow, preventing operational failures.
3. Flush Mount Fittings
Flush mount fittings are recessed into the surface of the equipment, providing a streamlined and unobtrusive option. These are ideal for applications where protruding fittings could pose risks.
4. Non-Return Fittings
These fittings ensure that the lubricant only flows in one direction, preventing backflow and maintaining consistency in lubrication. They are crucial for high-speed applications.
5. XL and Reduced Size Fittings
Available in various sizes, these fittings allow for compatibility with diverse machinery and operational spaces, ensuring that you have the right fitting for every application.
How to Choose the Right Central Lubrication System Fittings
Selecting the appropriate central lubrication system fittings necessitates understanding your specific needs. Here are several key factors to consider:
- Operating Environment: Assess the conditions in which the fittings will operate, including exposure to dust, moisture, and temperature extremes.
- Type of Lubricator: Ensure compatibility with the type of lubricant you are using, be it grease or oil.
- Flow Rate: Consider the flow requirements of your machinery to ensure that the fittings can deliver adequate lubrication.
- Pressure Ratings: Evaluate the pressure tolerance of your system; fittings must accommodate the operational pressures without leaking.
- Space Constraints: Measure the space available for fittings to ensure a proper fit without compromising performance.
Advantages of Using Central Lubrication System Fittings
Implementing central lubrication systems equipped with the right fittings offers a multitude of benefits, including:
- Reduced Wear and Tear: Consistent lubrication helps keep equipment parts smooth, thereby reducing wear and prolonging their lifespan.
- Improved Efficiency: Maintained machinery operates more efficiently, leading to lower energy usage and better productivity.
- Less Downtime: With well-lubricated systems in place, businesses can reduce unexpected breakdowns and maintenance periods.
- Consistency in Lubrication: Automated systems provide uniform lubrication across all areas, ensuring that no part is neglected.
Installation and Maintenance of Central Lubrication System Fittings
Proper Installation
Installation of central lubrication system fittings should always follow the manufacturer’s guidelines and best practices to ensure optimal functioning:
- Ensure Cleanliness: Install fittings in clean conditions to prevent contaminants from entering the lubrication system.
- Check Compatibility: Verify that all components, including fittings and hoses, are compatible in size and function.
- Tighten Connectors: Use the appropriate tools to ensure all connectors are securely fastened to prevent leaks.
Regular Maintenance
Routine maintenance is critical to keep central lubrication systems running smoothly:
- Inspect Fittings: Regularly check fittings for signs of wear or damage.
- Monitor Lubricant Levels: Keep an eye on lubricator levels to ensure consistent supply.
- Clean the System: Flush the system periodically to remove any contaminants that might impair performance.
Conclusion: Investing in Quality Central Lubrication System Fittings
In conclusion, central lubrication system fittings are indispensable for the efficiency and longevity of machinery in various industries. By understanding the different types of fittings available and selecting the right ones for your specific needs, you can significantly enhance the performance and reliability of your equipment. Choose quality fittings from reputable suppliers like fitsch.cn to ensure your lubrication systems function at their best, preventing costly downtime and repairs.
For more information on central lubrication system fittings, their applications, and purchasing options, visit our website: fitsch.cn.