Pressure Die Casting Factory: A Cornerstone of Modern Metal Fabrication
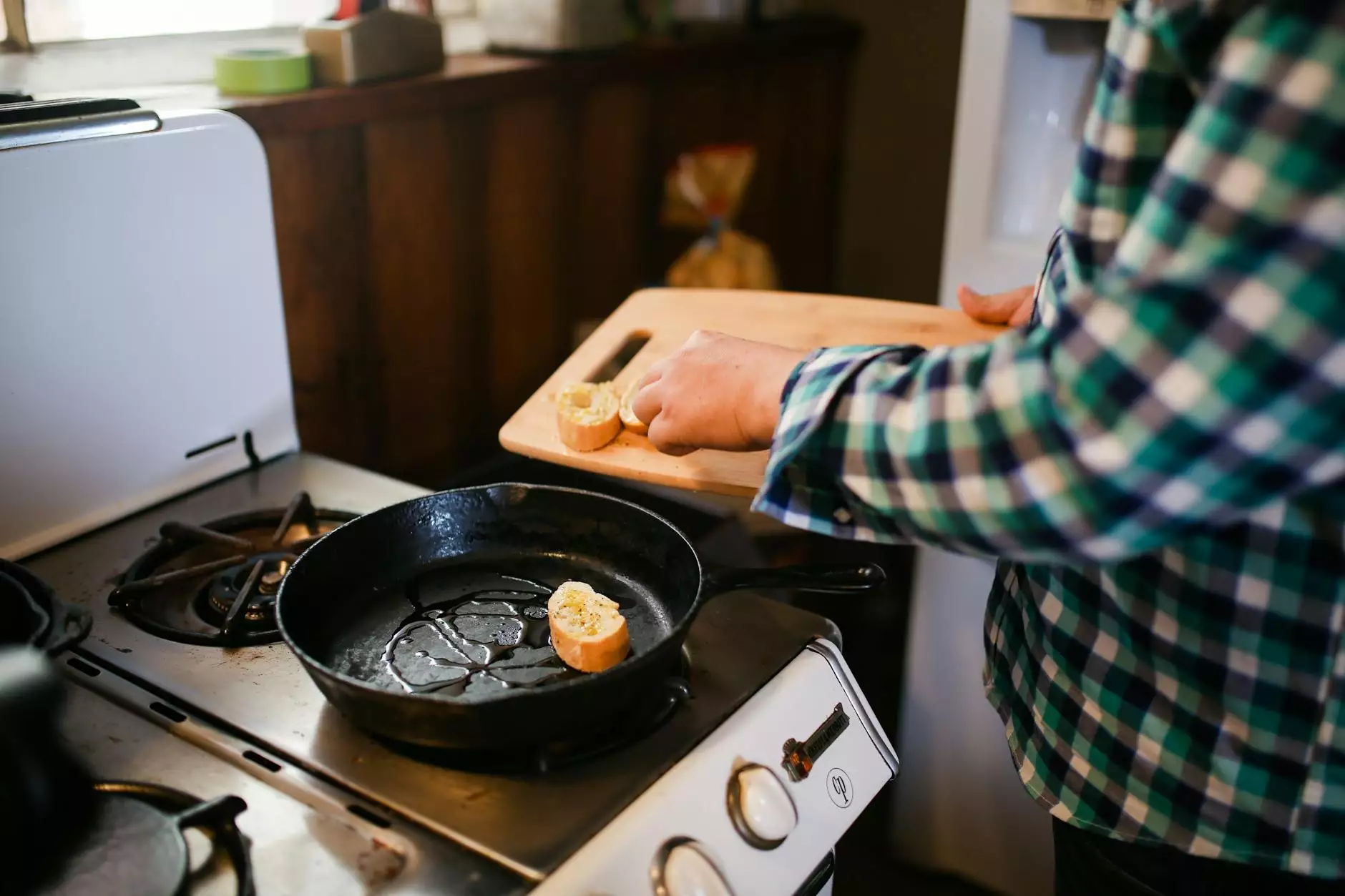
In the realm of metal fabrication, the role of a pressure die casting factory cannot be understated. This innovative process allows for the production of intricate and precise metal parts that meet the demanding requirements of various industries, including automotive, aerospace, and electronics. In this article, we will delve deeply into the functions, benefits, and practices of pressure die casting, ensuring you understand why this method is pivotal for your business needs.
Understanding Pressure Die Casting
Pressure die casting is a manufacturing process that involves forcing molten metal into a mold cavity under high pressure. This technique produces parts with excellent dimensional accuracy and surface finish. Here are the key components of the pressure die casting process:
- Molten Metal Preparation: The desired metal alloy is melted in a furnace, typically at high temperatures.
- Mold Creation: Molds are usually made from metal and are designed to withstand high pressure and temperature.
- Injection: The molten metal is injected into the mold under significant pressure, ensuring that it fills every crevice.
- Cooling and Solidification: After the metal fills the mold, it is allowed to cool, solidifying into the desired shape.
- Mold Removal: Once cooled, the mold is opened, and the cast part is ejected.
The Advantages of Using a Pressure Die Casting Factory
Choosing to work with a pressure die casting factory offers numerous advantages for manufacturers and businesses looking to scale operations effectively. Here's why you should consider this process:
1. Cost Efficiency
High-volume production using pressure die casting is often more cost-effective than other methods, particularly when producing large quantities of identical parts. The initial setup may require investment, but the long-term savings on material and labor can be significant.
2. Precision and Consistency
Pressure die casting provides excellent dimensional accuracy, ensuring that parts fit together seamlessly. The high pressure used during the injection process minimizes voids and defects, making it an ideal choice for components that must meet stringent tolerances.
3. Rapid Production Speed
The speed of the pressure die casting process allows manufacturers to produce parts quickly. Once the initial setup is complete, the cycle time for each part can be incredibly short—often just seconds. This rapid production capability is advantageous for businesses that need to meet tight deadlines.
4. Complex Shapes and Designs
Unlike other metalworking processes, pressure die casting can produce highly complex shapes that would be challenging or impossible with traditional machining. The flexibility in design offers greater creativity in part development.
5. Waste Minimization
Because molten metal is injected directly into the mold, there is minimal waste material produced during the casting process. This efficiency not only reduces costs but also contributes to a more sustainable manufacturing approach.
Applications of Pressure Die Casting
The versatility of a pressure die casting factory extends across various industries. Below are the principal applications where this method excels:
- Automotive Components: Pressure die casting is commonly used for parts like engine blocks, transmission housings, and structural components due to its durability and weight-saving benefits.
- Aerospace Parts: With the demand for lightweight materials and robust structures, the aerospace industry utilizes pressure die casting to produce critical components.
- Electronics Housing: Many electronic devices require precision-engineered housing that can be efficiently manufactured through pressure die casting.
- Industrial Equipment: Parts for various types of machinery benefit from the durability and precision that pressure die casting can provide.
Choosing the Right Pressure Die Casting Factory
When selecting a pressure die casting factory, several factors must be considered to ensure that you find a partner capable of meeting your specific requirements:
1. Experience and Expertise
Look for a factory with a proven track record in pressure die casting. An experienced team will understand the intricacies of the process and will be better equipped to handle any unique challenges that arise.
2. Quality Certifications
Ensure that the factory adheres to relevant industry standards and holds certifications such as ISO 9001 for quality management. These certifications reflect a dedication to consistent quality and customer satisfaction.
3. Advanced Technology
Modern pressure die casting factories should utilize state-of-the-art machinery and technology to enhance production efficiency and precision. Investing in the latest equipment can lead to better quality products and faster turnaround times.
4. Material Options
Different projects may require various metal alloys. A comprehensive factory will offer a range of materials, such as aluminum, zinc, and magnesium, to suit your specific needs.
5. Customer Support and Communication
Reliable communication and customer support are vital. Your chosen factory should be responsive and willing to provide updates throughout the manufacturing process.
Comprehensive Look at the Pressure Die Casting Process
To appreciate how a pressure die casting factory operates, let's take a more detailed look at each step of the pressure die casting process, from start to finish:
Step 1: Designing the Mold
The first essential phase involves designing the mold. The design should account for metal flow, cooling, and part ejection to ensure optimal casting. Engineers often use CAD (Computer-Aided Design) software to create accurate mold designs.
Step 2: Preparing the Metal Alloy
The choice of metal is crucial. For instance, aluminum alloys are favored for their lightweight properties and strength. The selected alloy is then heated in a furnace until it reaches the appropriate temperature for pouring.
Step 3: Injection of Molten Metal
Once the metal is molten, it is injected into the mold under high pressure, typically around 1,000 to 2,000 psi. The high pressure ensures that the molten metal fills all the mold cavities, even in complex designs.
Step 4: Cooling and Solidification
After the molten metal is injected, it quickly cools and solidifies. Cooling systems embedded in the mold may help in expediting this process and improving production efficiency.
Step 5: Mold Opening and Ejection
Once the metal has solidified, the mold is opened, and the newly formed part is ejected. Ejection pins are often utilized to ensure that the part is removed smoothly with minimal risk of damage.
Step 6: Finishing Processes
Post-casting, the parts may undergo several finishing processes, including machining, surface treatment, and inspection, to ensure they meet the required standards and specifications.
The Future of Pressure Die Casting
The future of a pressure die casting factory is bright as industries continue to demand high-quality, lightweight, and durable components. Advancements in technology, such as:
- 3D Printing of Molds: Enhancing the design capabilities and reducing lead times.
- Automation: Increasing efficiency and precision in production.
- Material Innovations: Discovering new alloys that offer improved performance characteristics.
These innovations promise to propel the pressure die casting industry forward, allowing factories like deepmould.net to continue serving their clients with cutting-edge solutions.
Conclusion
In conclusion, a pressure die casting factory is an indispensable resource for businesses looking to enhance their metal fabrication capabilities. By understanding the processes, benefits, and applications of pressure die casting, companies can make informed decisions that contribute to their success. With advancements in technology and a growing emphasis on efficiency and quality, this method will remain at the forefront of manufacturing for years to come.
If you seek reliable and high-quality pressure die casting solutions, deepmould.net is your ideal partner. Their experience, technology, and commitment to customer satisfaction set them apart in the competitive landscape of metal fabricators.