The Science Behind Cavitation in Centrifugal Pumps
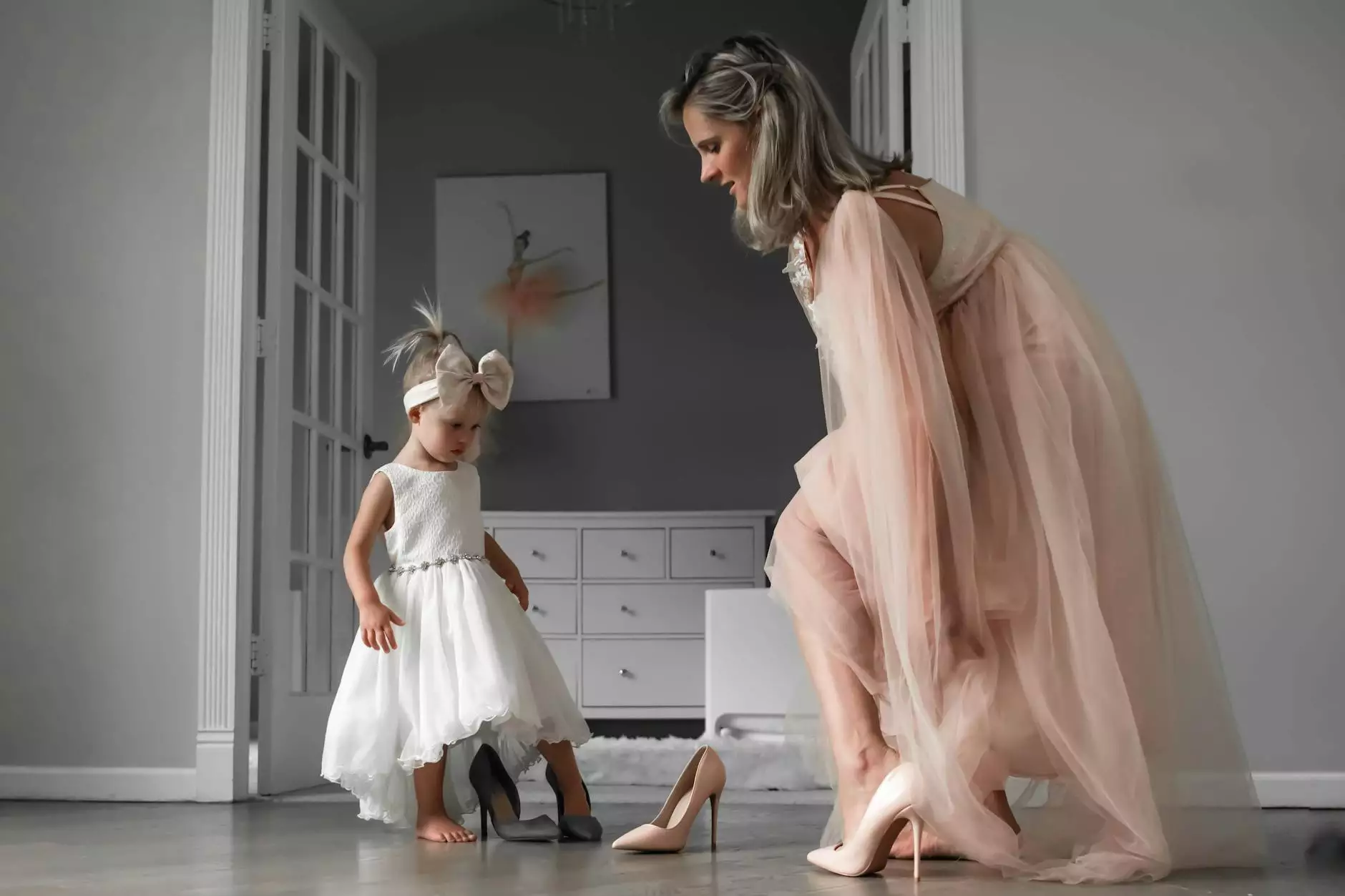
In the world of fluid mechanics and engineering, cavitation in centrifugal pumps is a phenomenon that engineers and technicians encounter in various industrial applications. Understanding what causes cavitation in centrifugal pumps is crucial to maintaining the efficiency and longevity of these essential machines.
What Is Cavitation?
Cavitation is a process in which vapor bubbles form and collapse in a liquid due to rapid pressure changes. In the context of centrifugal pumps, cavitation occurs when the pressure at the pump inlet drops below the vapor pressure of the liquid being pumped. This can lead to a range of detrimental effects on the pump system.
Causes of Cavitation
Several factors can contribute to the occurrence of cavitation in centrifugal pumps:
- Inadequate Net Positive Suction Head (NPSH): One of the primary reasons for cavitation is when the NPSH available is insufficient for the pump's requirements. This can happen due to improper pump sizing, high fluid temperature, or a rise in elevation.
- Clogged or Damaged Impeller: A clogged or damaged impeller can disrupt the flow of liquid through the pump, leading to localized pressure drops that trigger cavitation.
- High Pump Speed: Operating the centrifugal pump at high speeds can also increase the risk of cavitation, especially if the system is not designed to handle the resulting pressure conditions.
- Incorrect Pump Installation: Improper pump installation that results in air pockets or vortices can create conditions conducive to cavitation.
Impact of Cavitation
Cavitation can have serious consequences on the performance and reliability of centrifugal pumps:
- Erosion and Damage: The implosion of vapor bubbles near the pump impeller can erode the material surface, leading to premature wear and reduced pump efficiency.
- Noise and Vibrations: Cavitation is often accompanied by loud noise and vibrations, which not only affect the working environment but also indicate potential mechanical issues.
- Reduced Pump Efficiency: As cavitation disrupts the flow of liquid and causes pressure fluctuations, the overall efficiency of the pump decreases, impacting performance and energy consumption.
Preventing Cavitation
Effective prevention measures can help mitigate the risks associated with cavitation:
- Ensure Sufficient NPSH: Properly sizing the pump and system components to maintain an adequate NPSH margin is essential for preventing cavitation.
- Regular Maintenance: Routine inspection and maintenance of the pump, impeller, and associated components can help identify and address issues before they escalate.
- Optimize Pump Speed: Operating the pump within the recommended speed range and adjusting the impeller diameter can help reduce the likelihood of cavitation.
Conclusion
Overall, understanding the causes and effects of cavitation in centrifugal pumps is key to optimizing the performance and lifespan of these critical machinery in various industries. By implementing proactive measures and monitoring pump conditions, businesses can minimize the risks of cavitation and ensure smooth operations.
For expert advice and solutions related to centrifugal pumps and cavitation issues, trust Michael Smith Engineers - your reliable partner in Auto Repair, Farm Equipment Repair, and Structural Engineering.